Will Brexit mark a change in manufacturing methodology?

21 October 2019
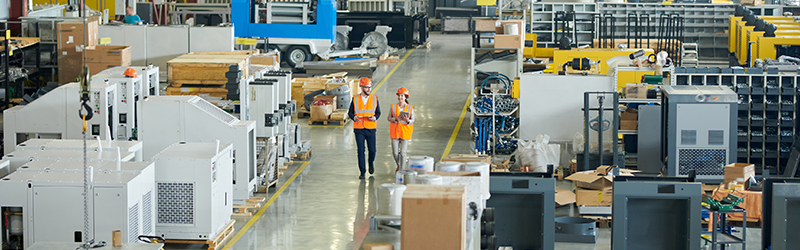
Every business controls its stock differently. But when it comes
to manufacturing, developing a supply chain designed around improving
efficiency, flexibility and response speed has always been the ultimate goal.
For many years, ‘Just in Time’ manufacturing has been the
overriding process to help businesses run such lean and efficient production
lines.
The idea was developed first by Japanese car manufacturers in the
1960s, who in turn were inspired by American supermarkets that keep their
shelves full but kept just enough stock to refill any spaces as customers took
items.
In a manufacturing scenario, the principle behind Just in Time is
making only what’s needed when it’s needed and in the quantity that is needed.
This provides many benefits, including low costs for inventory, quicker
response to change, repurposing of warehouse space, increased flexibility and
reduced waste.
Just in Time manufacturing has been the process favoured by most
manufacturers the world over ever since. But in Britain this lean and mean methodology
is coming under threat.
Brexit Stockpiling
While arguments over Britain’s future relationship with the EU
continue to rage on (with no decision on a deal at the time of writing), Brexit
has already had a significant effect on manufacturing methodologies as business
scramble to prepare for an uncertain future.
In fact, research earlier this year found that UK manufacturers
are stockpiling goods at the fastest pace on record[1].
The rapid stockpiling has been blamed on the lack of clarity involved with
Brexit and manufacturers being forced to make contingency plans for worst-case
scenarios.
Many UK manufacturers rely on European imports and are therefore
stockpiling materials for their production processes in the event of imports
becoming less frequent. The shift to keeping inventory high as opposed to low
represents a transition from Just in Time manufacturing to ‘Just in Case’
manufacturing.
Just in Case manufacturing means that manufacturers
hold a buffer stock of raw materials ready for production just in case they are
in demand or supply fluctuates.
With Brexit, this is an enforced change. Many UK
manufacturers are finding that European suppliers have reduced the frequency in
that they ship to UK.
Furthermore, if and when Brexit does occur, delays
at customs borders will likely cause problems for supply chains involved in UK
manufacturing.
With over 1,100 trucks crossing the Channel daily
transporting deliveries intended for UK manufacturing, delays at the border
could be disastrous for businesses that use Just in Time processes.
For example, Honda estimated that every 15 minutes
of customs delays would cost some car manufacturers in the UK up to £850,000
per year[2].
The extra time and staff that businesses could
require in order to complete paperwork or delays while goods are checked at customs
could mean that production lines are left empty and customers are left waiting.
Bright side
Of course, it’s not all doom and gloom as there are
some positives to the Just in Case methodology. Reduced clerical and purchasing
costs, lower unit price for buying in bulk and of course avoiding stock-outs
are just a few of the advantages of maintaining a higher inventory level.
But to make it a success, the Just in Case model
will require extra resources to maintain larger inventories.
The good news is that the latest technology can
help to meet this challenge and ensure that processes are still carried out in
an efficient manner so that warehouse space is used wisely, accuracy is
ensured, and staff receive clear instructions to keep the business moving.
Powerful rugged devices will be critical to achieving these aims in
a Just in Case scenario. As well as improving warehouse processes at an
individual level, the latest devices can seamlessly update management systems
to make the whole operation flow faster and with greater accuracy.
Even saving just a few seconds per task can translate into
meaningful efficiency gains and can go a long way towards achieving new
strategies such as lean manufacturing.
But businesses have to be able to rely on their devices if new
processes are to be successful. It’s vital that any investment in new
technology will consistently help drive innovation and increase efficiency.
A trusted technology partner can
advise on these issues and provide bespoke solutions for an
innovative and tailored approach to implementing real-time mobile computing
solutions into any organisation.
There’s no substitute for a partner
taking you through the steps to create the ‘best fit’ mobile computing solution
that will deliver real competitive advantage to your operational processes.
ABOUT THE AUTHOR - PETER MARSH
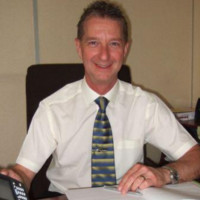
Peter joined TouchStar (formally Belgravium) in a sales manager role in 2001. Prior to joining the company, Peter held Partner and National Sales Manager roles within the parcel and logistics industries.
In 2011 Peter was promoted to Sales Director and is now actively involved in promoting the value of TouchStar’s Rugged Mobile Computing solutions to the warehouse, logistics, manufacturing and field service industries. When not involved in the business, Peter is a keen and enthusiastic football and cricket fan.
ABOUT TOUCHSTAR
With over three decades of experience within the development of
mobile computers for warehouse environments, TouchStar has the knowledge to
confidently offer mobile computing solutions to successfully addresses key
business issues.
TouchStar’s handheld, wearable, and vehicle-mounted mobile
computers are purpose-built to provide enterprise-level support for warehouse
management needs. From labour-intensive assembly tasks to fully automated
environments, TouchStar’s rugged mobile computers help reduce errors and
significantly increase productivity in manufacturing operations.
Whatever area of manufacturing you are involved in, TouchStar’s
rugged mobile computers provide the visibility of materials, parts and finished
goods flowing through your manufacturing operations.
TouchStar offers extremely competitive prices on all its devices
helping minimise procurement costs. TouchStar’s experts are just a phone call
away to help you choose the right products for your needs.
Visit our website or contact us to talk to our experts today.
[1] https://www.bbc.co.uk/news/business-47086920
[2] https://www.theguardian.com/politics/2017/nov/14/honda-uk-warns-mps-of-consequences-of-leaving-eu-customs-union