Warehouse Blog: Managing seasonality - The pressure is on to maximise profits.

05 December 2018
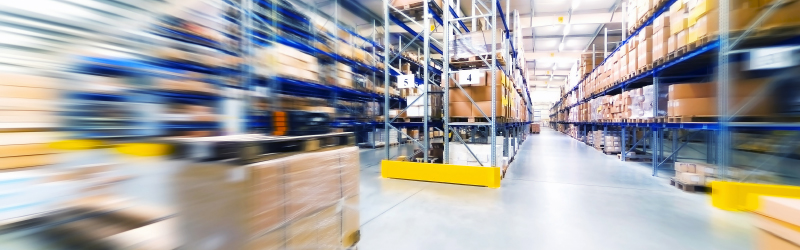
Managing
seasonality in the warehouse
With Black Friday behind us, the
year’s busiest retail season is well and truly here. For many businesses, the
countdown to Christmas holds more commercial opportunity than any other time of
year, so the pressure is on to optimise processes and maximise profits.
When it comes to
warehouses, meeting and exceeding the demands of the season is becoming more
challenging from one Christmas to the next. Online shopping is accounting for a
larger segment of all Christmas spending year on year, and isn’t slowing even
when the big day arrives – in 2017, UK online retail sales on Christmas Day were up five percent on 2016’s total of £794 million.
So, over the next
month or so, your warehouse is likely to be under more operational strain than
ever. Simultaneously ensuring you have the stock on hand in order to fulfil
orders quickly while also managing storage space efficiently is a balancing
act, and one that Christmas makes even trickier. Here’s how your warehouse
management system and associated devices should be helping you face it head on.
Put your historical seasonal data to
use
Looking back at
festive seasons gone by can yield more than just profit margins to beat;
drilling down into data about what sold and when, can reveal trends you can use
to better plan for this Christmas. Recurring spikes relating to certain items or
types of products give a good indication that they will be in high demand again
this year, so factoring this in ahead of time can help avoid stock shortages.
Of course, this kind
of predictive planning is only possible when you have accurate and intuitive
warehouse reports at your disposal. A management system should track stock as
it moves through your warehouse, with every stage of its journey creating a
data footprint that enables you to easily spot useful sales patterns as they
emerge.
Keep track of every last item
This level of insight
requires data gathering right at the heart of your operation - on the warehouse
floor. Your warehouse team need devices that effortlessly record relevant
information about your stock with a simple scan as they go about their duties,
which can then be fed into a central data hub and used to identify seasonal
trends.
Warehouses are
demanding working environments though, so standard scanning hardware is
unlikely to be fit for purpose. Ergonomic and easy-to-use rugged handheld and
truck-mounted computers give your warehouse team (even temporary Christmas
support staff who may lack experience) the capacity to work with maximum accuracy,
speed and efficiency, allowing them to swiftly and wirelessly generate the data
you need to highlight fluctuations in demand.
Don’t let returns ruin your profit
margin
More stock shifted
during the run-up to Christmas inevitably means a higher number of returns
after the 25th has been and gone. There’s not much you can do about an
increase in returns – today’s consumers often shop on the basis of their
ability to return goods for free – but your warehouse management software
should help you minimise their impact.
Strict stock control
helps to make reintroducing returned items into your inventory smooth and
seamless, and enables you to see at a glance whether you will have to move
things around to make room. What’s more, where possible, the level of
visibility a warehouse management solution affords should also allow you to
reallocate returns to fulfil back orders, negating the need to restock them
first.
Pre-empting how
seasonality will affect warehouse supply and demand can give your business the
tools to master the pre-Christmas rush. With the right warehouse management system, the festive season can allow your operational
processes to come into their own.