Magnavale: Providing Streamlined Supply Chain Services and Traceability with Real Time Data Capture.

28 July 2021
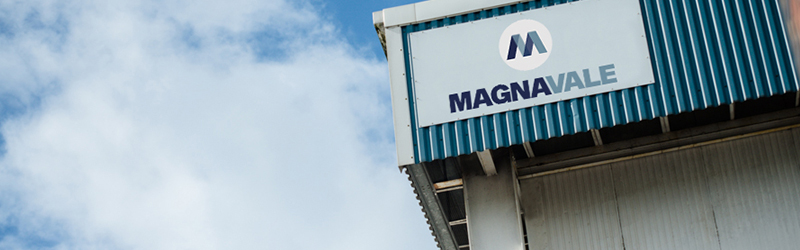
A choice partner for major
food manufacturers and retailers, Magnavale strive to provide a just-in-time-service
through a comprehensive portfolio of temperature-controlled solutions. Facing a
fast turnaround and the challenge of providing reliable, streamlined operations,
the business turned to TouchStar Rugged Mobile Computers to facilitate real
time benefits within their Chesterfield based Group Headquarters.
The Business
With over 1.95 million square
feet of warehouse space and more than 200,000 pallet spaces across
multi-temperature regimes nationwide, Magnavale is the choice partner for major
food manufacturers, importers and retailers for temperature-controlled storage
solutions.
Providing BRC certified
storage and distribution facilities across their 3 strategically located sites in Chesterfield, Scunthorpe and
Warrington, their services include temperature-controlled storage for various
food products, blast freezing and labelling through to microwave tempering and
more.
Established for over 30
years, the business has gone from strength to strength. Since the three sites
merged under the Rick Bestwick brand in 2016, the business continued to thrive
and grow, despite the pressures from Brexit, Covid and industry wide changes to
legislation. Whilst known for quality and reliability, the decision was made to
proceed with a name that would unite the businesses and the future it would
strive towards, Magnavale.
Value
Added Service
With several
systems in place to support the supply chain requirements of their end users,
Magnavale recognise the value technology adds to their operational processes. Martin
Tipper, Group IT Manager comments, “As a business, our aim is to facilitate a full range of streamlined
supply chain services that reduce costs and increase efficiency. To ensure we minimise product handling,
provide traceability and have as short a supply chain as possible, we need to
have the systems in place that are not only reliable, but that would be both
futureproof and scalable to support our growing operations”.
The Challenge
Magnavale’s Group
Headquarters, strategically placed in Chesterfield, houses over 500,000 sq.ft
of warehouse space and more than 50,000 pallet locations. The main use of data capture within the operation was
to facilitate the movement of pallets within their cold store put away and
picking operations. With their existing data capture equipment now unsupportable
Magnavale were concerned about the costs and potential impact on service levels.
As a forward-facing company, Magnavale made the decision to upgrade the RF
equipment within their Chesterfield operation, ensuring a futureproof and
scalable solution was selected to support future growth plans.
The Solution
The
challenge for Magnavale was to source some new RF devices that would be able to
integrate directly into their existing WMS system. Following an extensive
research and testing process, Magnavale turned to leading UK manufacturer
TouchStar Technologies, selecting their fit for purpose TS8000 handhelds and
TS7000 truck mounts for the upgrade.
The TS8000
offered several advantages for the users on site. With its optimally
positioned hard capped keys, the TS8000 was the perfect device for Magnavale’s
scan intensive warehouse operation. Not only that, the availability of a hot
swappable battery, guaranteed continuous operation and reduced downtime,
maximising output, and increasing workload efficiency. For the truck mounted
requirement, the TS7000 provided a fit for purpose device, integrating rich
functionality into an ergonomic and compact design with rugged features such as
polycarbonate plastic alloy casing and a sealed membrane keyboard.
Following the initial
dialogue and selection, TouchStar worked closely with Magnavale to manage the
upgrade, covering everything from specification through to testing
compatibility with their core WMS, go live and ongoing support. To facilitate
the real time data capture, TouchStar needed to ensure full connectivity with
Magnavale’s existing Wi-Fi network.
Results and Benefits
At the point where the system went live, TouchStar engineers were on hand
throughout, ensuring the correct configuration and set up of the new scanning
devices. The support of TouchStar
prior to the system going live resulted in a successful rollout of the new
devices. Rugged and reliable, both devices fulfilled Magnavale’s requirements
for high-speed scanning and data capture within what can be a challenging cold
storage environment.
Martin adds, “TouchStar
provided a competitively priced and locally supported solution. The overall
system implementation went extremely well, and the devices have proved to be extremely
reliable. Despite the external business challenges such as Brexit and Covid, we
have no doubt that the benefits brought about from the RF upgrade have had a
hugely positive effect on our operations. Investing in UK manufactured, and
locally supported devices have ensured that we maintained high service levels
and seamless operations. Operating a reliable system, we have removed the costs
we typically associate with downtime. We
are excited about the potential uses of the devices look forward to working
with TouchStar on future projects”.
The Future
Since the implementation,
Magnavale have continue to innovate and grow, becoming one of the first cold
store networks in the UK to offer segregated, temperature controlled, storage
solution’s specially for plant-based foods. With the new directions the
business is taking, Magnavale continue to evolve and develop their operations
having confidence that the technology they have invested in will continue to
meet the business’s needs both now and into the future.