The Elastic Warehouse - White Paper

14 February 2020
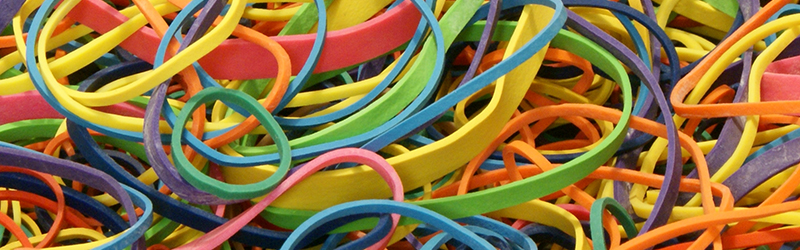
Because when the world is constantly changing, you need to flex for success
More than ever before,
organisations are challenged to generate greater efficiencies and better
performance because consumers are demanding more.
Once upon a time, people used
to take a trip into town to purchase anything they needed. But life isn’t like
that anymore. Today, our lives revolve around convenience, so habits, such as
online shopping have become more prevalent – 57% of consumers actually prefer
to shop online, with a third stating the primary reason is their ability to
shop 24/7(1).
“Online sales continue to
increase 64% year-on-year(1), and by 2024, online shopping is forecast
to account for 19.3% of total retail spend (2).“
It’s driving demand for different
delivery methods, such as ‘buy now pay later’ schemes, and ‘click-and-collect’,
which 58% of Internet users aged between 18 and 25 have tried(3).
But it’s also changing expectations.
Less than 5 years ago, online
shoppers were happy to wait 4.8 days for a package delivery – today, it’s just
2 days(4). Online retailer Amazon has played a huge part in making
2-day shipping the ‘norm’, and for its Prime members, the expectation is greater
still - next, or even same-day, delivery.
But enabling your business with
the logistics required to meet the demands of online shoppers isn’t that simple.
And it’s not just retail
feeling the pain. Take the pharmaceutical sector responding to demand for drugs
in health care, to the manufacture of construction materials required to meet
the surges of house building, through to components for electronics. Industries
across the board are having to find ways to be more agile and get more out of
their investment in warehousing and technology.
The lack of available warehouse space
According to data from Logistics
Management and Peerless Research Group, on average warehouses are operating at
68% capacity - although 15% said they were full, with a further 19% somewhere
between 81%-99% (6).
Despite the industry’s best
efforts, the hard truth is that the current growth rate isn’t enough. Demand for
warehouse space has outpaced supply since 2010(7), with demand set to
increase by 53% over the next 2 years(7). Plus, peak times of year
already cause a surge in demand – everything from Christmas when a typical
household spends an additional £800 in December8, to political
uncertainty related to Brexit which has created stockpiling of critical
medicine, foods and drinks, and raw materials.
Assuming you manage to secure
the space you need, then you will have a number of other practical hurdles to
overcome. The four principal ones are:
Updated delivery requirements
65% of retailers are planning
to offer a same-day delivery service within the next 2 years to meet consumers’
growing demands(9). But achieving that delivery window requires huge
logistical changes in the warehouse. And with 90% of consumers now tracking the
delivery status of their order(10), you need to be set up to provide
the real-time status they crave. If you are involved at any point along the
supply chain – from raw materials to finished goods, you’ll feel the impact of
the consumer demand.
Accounting for reverse logistics
30% of all products ordered
online are returned, compared to just 8.89% in brick-and-mortar stores(11).
It’s costing retailers 8% of their total sales(12) since reverse
logistics requires additional labour to process the returns, and about 20% more
warehouse space(13). When you consider that only half of returned
items can be resold at full price(14), planning how you deal with
returns and setting your warehouse up accordingly really is crucial to maintaining
a healthy profit margin.
Trading globally
Trade deals control the flow
of goods into the country. But during times of political uncertainty, issues
arise - ahead of the December 2019 General Election, three-quarters of
warehouse owners claimed to have no available space after retailers stockpiled
goods amid uncertainty around Brexit(15). And then there’s the
workforce itself. Here in the UK, EU workers currently make up 13% of the entire
logistics workforce, but declining EU net migration has contributed to a 43%
rise in job vacancies over the past couple of years(16). Mitigating
these risks with appropriate controls is essential to surviving the global
markets.
End of life tech
Despite Microsoft phasing out
its Windows Embedded Handheld operating system (OS), 50% of decision makers
expressed that they would remain with this legacy technology after its end of
life phase(17). Without security patches or software updates, these organisations
are exposed with attackers actively targeting the known security vulnerability.
Therefore, transitioning from legacy Windows is a business necessity, and there
really is no better OS than Android™ since it’s already used in 80% of
smartphones around the world(18).
Logistics managers now have a complex problem
The puzzle is now about how to
manage all these challenges while maintaining the more predictable day-to-day
demands of the warehouse environment.
So how do you:
·
Support the introduction of new shopping
channels,
·
Have the flexibility to manage more volatile
‘trends’ until they are a proven commodity,
· Hit Service Level Agreements (SLAs),
·
Avoid introducing any risk to the supply chain,
·
Deliver it all within the same confines of the
existing warehouse
and still maintain a healthy
bottom line?
With a finite amount of
resource, investing millions in building state-of-the-art facilities to create
new super hubs is probably out of the question for most organisations. Some might
look into more modest expansion. But with annual costs for warehouse space
typically ranging from £50,000 to £300,000 per square meter(19), the
cost may be prohibitively expensive. While others will focus on re-engineering
and streamlining their existing facilities in an attempt to create efficiencies
in the supply chain.
But there is another option.
The Elastic Warehouse.
The Elastic Warehouse
An alternative concept is the Elastic
Warehouse, which allows organisations the flexibility to bend, grow or shrink
in line with the demands of the supply chain at a moment’s notice, all within
the parameters of their existing property.
The approach provides
companies with:
·
The flexibility to meet fluctuations and
unplanned changes to demand.
·
The potential to take on more contracts and not
forfeit seasonal work.
·
Financial stability, accounting for
fluctuations in a far more controlled way.
·
Increase workflow without jeopardising SLAs or
impeding regulatory standards.
·
Improved staff efficiencies from well organised
working conditions.
Achieving it is reliant on
adopting a new model that best suits your operations and your future ambitions,
along with the underlying supporting technology.
The 4 models to create the Elastic Warehouse
1.
Elastic Overheads: existing
tech, people and warehouse space investments work harder.
2.
Elastic Outsource: outsourcing
warehousing and distribution of key seasonal lines for a finite period.
3.
Elastic Tech: a
complete technology-lead implementation.
4.
Elastic Blend: cherry
pick elements of the first 3 approaches for the ultimate financial and
operation control.
Model 1. Elastic Overheads
Using the latest technology to
optimise all assets, including technology, people and warehouse space, this
model focuses on how to make your existing investments work harder.
At its core sits a process
management system, which is coupled with handheld technology used to check in,
find, pick and allocate stock as the warehouse expands. And it works best when
the scheduling tools link directly to the ordering and fulfilment systems. Now
you can accurately forecast stock levels and demand at any time and plan your
resourcing appropriately.
Choosing to adopt an Elastic
Overheads model is likely to include the following initiatives:
·
Evaluate employee demographic: to
understanding the language differences and identify training gaps, which need
addressing to improve productivity.
·
Take an inventory: to identify
equipment requirements, which could include anything from forklifts to picking
arms, totes, racking and shelving.
·
Technology review: to
check that your hardware, applications and work management tools are agile
enough to cope with fluctuating demand.
·
Special considerations: if
you’re adopting voice picking technology, consider that your workforce might not
have a good command of English so chose the right language settings.
· Process review: to
eradicate obsolete processes, improve broken ones, and introduce new ways of
working.
·
Device review: to
ensure you have sufficient devices to deal with peak times, and enough chargers
so new shift workers never run out of power.
·
Wireless site survey: to
ensure you optimise your wireless coverage across the warehouse, which can get
blocked by racking.
Model 2. Elastic Outsource
Adopting this approach
maintains the status quo of the day-to-day operations. It ensures the existing
operation remains focused on the core lines, by using a third-party to take on
the seasonal demand for a finite period.
The technology is integrated
easily with the third-party provider to ensure the management teams have access
to key information, regardless of where the stock is geographically, or which
company is managing that stock.
Choosing this model is
particularly useful when:
·
The extra capacity is required for a finite
period of time, for example, over Christmas.
·
The day-to-day demand for core lines is steady
and already deemed to be at full capacity.
·
There are strong economics, or the benefits
outweigh the cost.
·
The suppliers of the seasonal lines are
different to those of the core lines.
Model 3. Elastic Tech
This approach is concerned
with using the existing footprint more efficiently by implementing technology
across the whole supply chain to bridge any gaps. It’s ideal for bigger
operations that manage large volumes of goods, or disparate warehouses and
distribution centres.
Typical technology
implementations include:
·
Handheld data capture: using
devices to quickly scan items into the warehouse and send them to the
designated storage area.
·
Warehouse Management Systems (WMS): using
barcodes to identify items quickly and easily within the warehouse, with orders
fulfilled with 100% accuracy.
·
Applications: to provide
real-time information about the speed of operations, as well as uncovering and
alerting management teams to bottlenecks.
·
Mobile printers: to
produce customer order/address labels that can be put onto pallets as soon as
they are picked, which avoids delays.
·
Integration:
connecting the dots between all other enterprise systems with those used by the
retailer and supplier.
Model 4. Elastic Blend
For most logistics distribution
centres, the Elastic Blend is the best way forward, since it takes the best of
all the previous 3 models; adopting and implementing the latest technologies
are complemented by improved processes and supported by trained people to
deliver the best outcome.
It’s best suited to larger
operations that:
·
Accommodate 24-hour delivery schedules for
inbound vehicles.
·
Have the capability to integrate their systems
into supplier and customer systems.
·
Need to retain control of the end-to-end supply
chain no matter the scale of the extra demand.
·
Rely on efficient distribution and stock
transfer for various delivery/collection services.
·
Have investment readily available for hardware
and training.
·
Demanding SLAs with hefty financial penalties.
5 steps to identify the best model for your organisation
Taking the decision to adopt
an Elastic Warehouse approach sets the path for growth, creates the opportunity
to take on larger contracts and helps to differentiate or diversify your
offering. But achieving it requires careful planning:
Step 1: perform a gap analysis
You need to identify where
your ‘problem areas’ are, before you can start planning how to address them
appropriately. It’s important to be clear on what you need the Elastic
Warehouse to achieve for your business.
For example:
·
Do you want to diversify and move from frozen
into perishables, or introduce more seasonal ranges into your FMCG operation?
·
Do you want to take a slice of the
international export market?
·
Do you want to specialise in a particular high-risk,
but high-profit market?
·
Do you want to offer more choice to customers
as to how and when they receive orders with services, such as click-and-collect?
Step 2: map your processes
You need to identify ‘what
should be happening in your supply chain’ versus ‘what is actually happening in
your supply chain’. This allows you to identify current points of weakness,
processes in need of improvement, and areas where your
technology/staff/facilities aren’t being used to their full potential.
Step 3: map the physical layout
Regardless of the model you choose,
one of the key components to creating an Elastic Warehouse is making sure that
the physical layout of the warehouse is correctly specified. Software can help
you to play around with the configuration and get the racks laid out in a
logical order for goods inward receipting and putaways, bulk storage and
quality or quarantine checks areas, and goods out.
Step 4: consider your SLAs
Moving towards an Elastic
Warehouse model will require change that could affect the SLAs you currently
have in place. Consider if/how you need to update them, and whether it’s
possible to deliver a better/different service that differentiates your
organisation.
Step 5: introduce a WMS
Using a WMS you can eradicate
many issues by giving structure and sequence to how stock is organised and
managed within the warehouse. Adopting software to assist, rather than
traditional paper-based systems, enables you to significantly improve the
accuracy of your operations, while leveraging automatic identification and data
capture for better reporting.
In the spotlight…
30% of errors are due to the
operator picking the wrong item, but by integrating technology into this
process, you can eliminate those inefficiencies. There are 2 main types of
picking technology to choose from:
1.
Radio Frequency Scanning: using
handheld scanners with built-in screens, which use barcodes to identify every
SKU in the warehouse. It offers an expected pick rate of 50-190 lines per hour,
accuracy of up to 99.5% and savings of up to 25%.
2.
Voice: using headset
technology where an operator informs the user of where to go and how many items
to pick. It offers an expected pick rate of 175-275 lines per hour, accuracy of
up to 99.97%, and efficiency savings of up to 25% over Radio Frequency
Scanning.
We can help you plan for success in the Elastic Warehouse
Every organisation is
different, comprising varying warehouse footprints, geographies, skills,
technologies, customer profiles and locations, as well as regulatory and
perhaps cross-border legislation and compliance.
Embarking on a programme of
change comes with many challenges. And understanding the pitfalls and planning
to manage them is a critical part of the Elastic Warehouse puzzle. But get the
balance between technology, process and people right, and the rewards can be
great.
While many organisations set
out with the best of intentions - some even getting as far as creating a new
organisational blueprint - sadly for many companies it never becomes a reality
as the change programme is deemed too ambitious.
Yes, building an Elastic
Warehouse is an ambitious undertaking – but it enables ambitious strategies to
be realised. The Elastic Warehouse really is the best way for any company to
grow its customer base, open up new markets and unlock new territories, while
returning real value back to its shareholders – and we can help you.
Well experienced in this arena,
we can work with you to determine which model is best for your organisation,
and how to:
·
Align it to a 3 or 5-year plan, which ensures a
healthy return on your investment.
·
Ensure that the enabling technology is fully
adopted across the business.
·
Help your people to see their future role in
the new Elastic Warehouse, and how the proposed changes improve their working
day, give them the ability to achieve more and fulfil their own potential.
ABOUT THE AUTHOR - PETER MARSH
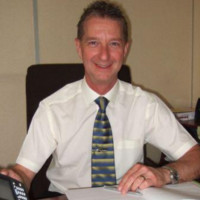
Peter joined TouchStar (formally Belgravium) in a sales manager role in 2001. Prior to joining the company, Peter held Partner and National Sales Manager roles within the parcel and logistics industries.
In 2011 Peter was promoted to Sales Director and is now actively involved in promoting the value of TouchStar’s Rugged Mobile Computing solutions to the warehouse, logistics, manufacturing and field service industries. When not involved in the business, Peter is a keen and enthusiastic football and cricket fan.
Sources:
1 "25 Stats on
Consumer Shopping Trends for 2019", Digital Doughnut, https://www.digitaldoughnut.com/articles/2019/may/25-stats-on-consumer-shopping-trends-for-2019
2 "UK online
shopping spend to grow 30% by 2024", Retail Insight,
https://www.retail-insight-network.com/features/uk-online-shopping-growth/
3 "Six Consumer
Trends to Watch in 2020", Ground Truth,
https://www.groundtruth.com/insight/consumer-trends-to-watch/
4 "How Consumer
Hunger for Two-Day Delivery Impacts Small Businesses", Clutch,
https://clutch.co/logistics/resources/how-two-day-delivery-impacts-small-businesses
5"Online
shopping drives demand for warehousing space", BBC News,
https://www.bbc.co.uk/news/business-45210148
6 "50 warehouse
automation stats you should know",
6 River Systems,
https://6river.com/warehouse-automation-statistics/
7 "Warehouse
supply rises but still can't match urban demand", Supply Chain, Drive,
https://www.supplychaindive.com/news/warehouse-shortage-supply-demand-CBRE/548182/
8 "How much do
we spend at Christmas?", Bank of England,
https://www.bankofengland.co.uk/knowledgebank/how-much-do-we-spend-at-christmas
9 "The
Importance of Same Day Delivery – Statistics and Trends", invesp,
https://www.invespcro.com/blog/same-day-delivery/
10 "7 Common
Shipping Questions and How to Prepare Before They're Asked", Shopify,
https://www.shopify.co.uk/blog/common-shipping-questions
11 "E-commerce
Product Return Rate – Statistics and Trends", invesp,
https://www.invespcro.com/blog/ecommerce-product-return-rate-statistics/
12 "The Point of
No Return – How Reverse Logistics Is Changing the Game", SmartConsign,
https://www.smartconsign.co.uk/2017/12/07/point-no-return-reverse-logistics-changing-game/
13 "Reverse
Logistics Boost Warehouse Sector", Supply & Demand Chain Executive,
https://www.sdcexec.com/warehousing/news/21040353/reverse-logistics-boost-warehouse-sector
14 "Future-proof
your reverse logistics", KPMG,
https://assets.kpmg/content/dam/kpmg/id/pdf/2017/08/id-future-proof-reverse-logistics-2august.pdf
15 "UK warehouse
space nears capacity as firms stockpile for Brexit", The Guardian,
https://www.theguardian.com/politics/2019/jan/21/uk-warehouse-space-nears-capacity-firms-stockpile-for-brexit
16 "Freight
Association Opens Consultancy Arm and Speaks Out on Migrant Workers",
Handy Shipping Guide,
https://www.handyshippingguide.com/shipping-news/freight-association-opens-consultancy-arm-and-speaks-out-on-migrant-workers_12606
17 "HOW TO
PREPARE FOR YOUR MIGRATION FROM WINDOWS CE TO RUGGEDIZED ANDROID… 20 QUESTIONS
ANSWERED", Honeywell,
https://www.honeywellaidc.com/en-gb/blog/2019/september/migration-ruggedized-android
18 "WAREHOUSE
HANDHELDS FLOCKING TO ANDROID AS WINDOWS MOBILE SUPPORT ENDS", Barcoding,
https://www.barcoding.com/blog/warehouse-handhelds-flocking-android-windows-mobile-support-ends/
19 "Rental
prices of prime retail warehouses in selected European cities as of 3rd quarter
2018", Statista,
https://www.statista.com/statistics/431712/retail-warehouses-real-estate-prime-rents-europe/