How Has COVID-19 Impacted the Connectivity of employees in the Logistics industry

07 March 2022
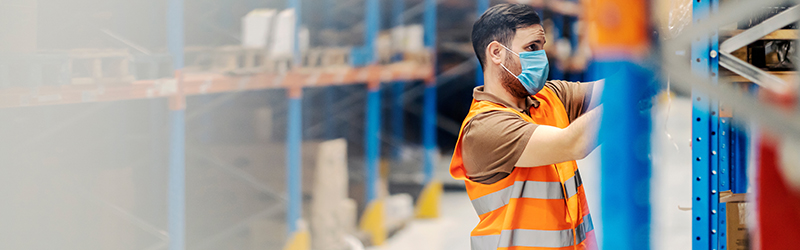
As everyone has experienced in one way or another, COVID-19
has caused mass disruption around the world. Although we’re starting to emerge
from the grey cloud it cast and can start seeing the light again, there are
some ways in which the coronavirus continues to impact businesses and their
workforces.
In the logistics industry, the past two years have
introduced a whole range of challenges to both suppliers and customers. Trying
to manage the supply chain, availability of products and changes to working
conditions have put pressure on everyone, highlighting existing issues as well
as creating new ones. How employees interact and connect with the business and
colleagues has also changed, with many more working from home and those employees
on-site needing to keep their distance from each other.
How COVID-19 affected the logistics industry
Although those working within supply chains were deemed to
be key workers, supplying much-needed PPE and food, amongst other items, businesses
have still had to contend with self-isolation and sick leave. This has put more
emphasis on the supply chain, but with fewer people.
Any staff within the industry that can work from home have
also been encouraged to do so. Therefore office staff, including management,
have been adjusting to managing operations from afar, relying on technology to
keep the wheel turning and minimising disruption.
Technology keeps everyone connected
There are many ways that technology can be used to keep
employees connected and a business running smoothly. Within the logistics
industry, warehouse management systems (WMS) and rugged devices are key to this
and have supported many businesses during the pandemic.
A warehouse management system is a piece of software that gives
businesses visibility over their inventory and helps to manage supply chain
fulfilment processes from warehouses to distribution to customers. This could
include managing stock levels, inventory management, order picking and stock
location amongst other capabilities. All this data is fed into a system by
on-site staff and can be accessed by anyone (with the right credentials and
permissions), including management at home. During COVID-19, this has enabled
management off-site to continue working and managing the supply chain.
Rugged devices are an important part of the supply chain
within warehouses and distribution centres. Rugged devices such as handhelds,
truck mounts and wearables can capture data by scanning barcodes, using RFID
capabilities and printing labels to enable warehouse staff to fulfil orders
effectively and efficiently. All this data from picking, shipping and inventory
are then fed into the back-office WMS and other business software. These rugged
devices have enabled home workers to have greater visibility on how workers on
the ground are doing, without being there in person.
Technology during the pandemic has not only kept the wheels
turning but has also helped to reduce the admin side of the supply chain
between on-site and off-site staff including:
- Confidence the data is reliable as there is less
human error
- Cutting down on physical paperwork
- Reducing unnecessary communication
- Streamlining processes
All this has ensured that the logistics industry and supply
chains have remained resilient and as efficient as possible during the
challenging times, keeping employees connected despite the challenging
circumstances.
What’s the future of the industry?
The fire-fighting nature of the past two years has meant
that businesses have not had a chance to stop to think, and instead the focus
has been on getting the job done. As the major threat of COVID-19 seems to be
coming to an end, and normality is returning, it’s now time to reflect on the
impact of the pandemic on the logistics industry in the long term.
For technology, this includes investing in upgrades and more
hardware which will assist businesses going forward. There has been little time
for those in logistics to update existing hardware or systems or invest in new
technology. This is now key to ensure the business can continue operating
effectively and to continue to drive efficiencies where possible.
Find out more
As technology continues to play a big part in keeping
employees connected and work continues to be carried out effectively, it’s
important that companies ensure their technology is kept up to date and that
all employees have access.
Here at TouchStar Rugged Computers, we work hard to ensure
our technology can be used to better connect employees on-site with those working
from home. We offer a complete range of wireless network services as well as a
dedicated support team. Get in touch to
learn more.
ABOUT THE AUTHOR - PETER MARSH
Peter joined TouchStar (formally Belgravium) in a sales manager role in 2001. Prior to joining the company, Peter held Partner and National Sales Manager roles within the parcel and logistics industries.
In 2011 Peter was promoted to Sales Director and is now actively involved in promoting the value of TouchStar’s Rugged Mobile Computing solutions to the warehouse, logistics, manufacturing and field service industries. When not involved in the business, Peter is a keen and enthusiastic football and cricket fan.