Is Automation Ready To Take On The Cold Store

11 June 2019
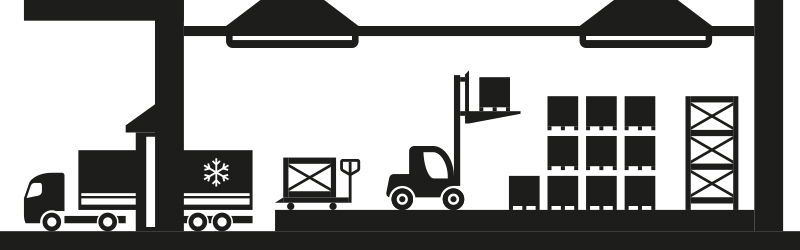
Across the logistics industry more and more tasks are becoming automated. Often taking over some of the more menial tasks, these automated processes have become key to streamlining many operations and improving accuracy.
But when it comes to highly controlled environments with requirements around temperature, can automation provide the same benefits or is human interaction needed to ensure the quality of an operation?
In cold store, maintaining a slick supply chain is crucial to ensuring the freshness of perishable products. In today’s world businesses also have to be incredibly flexible to deal with consumer demand, myriad delivery options and the diversity of products they offer.
Can automation be trusted to achieve the perfect cold store operation? Or has the technology not developed sufficiently enough in this area to warrant the risk and cost of establishing an automated system?
And what about rugged mobile computers? Technology in rugged devices is developing just as quickly. Can the latest mobile devices help staff in cold store to become more efficient and effective without the need for an automation overhaul?
In this article we will weigh up some of the pros and cons of each approach to help understand how cold store environments can be improved and enhanced in the coming years.
Automation for cold stores
The business case for implementing automation in any warehouse environment is strong. Demand is rising, workforce numbers are falling, faster processing is necessary and accuracy is paramount.
Automation offers solutions for all these issues.
Automated systems are also customisable and can be scheduled to operate outside normal working hours to meet deadlines or requests that would normally be outside of a business’s capabilities.
But in cold store it’s usually the accuracy which is key, as automation dramatically reduces the risk of any spoilage. Even your best staff can make the occasional mistake, but automation can take accuracy to new heights.
Damage to products, waste and energy savings can’t be overlooked, especially as companies strive to improve their environmental footprints. Many cold storage businesses have found themselves in a position where they are considering if changes need to be made to the traditional warehouse and distribution systems that they have come to rely on.
But fully automating an operation is a risky and costly business. Initial expenditure can be very high depending on the size of an operation and there’s no guarantee that implementing an automated system will pass hassle-free.
Then there’s the additional maintenance and upkeep to consider, and that’s before mentioning the management system that will need to be put in place to control and review the new technology.
However, there is the option of re-training staff who may have had their usual tasks replaced by automated systems. They could instead learn how to manage automated system, acting on alerts and fixing any issues and generally overseeing a new, more productive operation.
Rugged mobile computers in the cold storage industry
Just as technology around automation is developing rapidly, so too is the technology that staff hold in their hands.
Of course, it’s simply not a case of taking the latest consumer grade devices into temperature-controlled environments. Modern rugged devices are specially made to not only deal with the cold but also to help the staff that use them to be more effective.
Internal heat sources, seals designed to prevent condensation and high-performance batteries are just some of the features that help rugged devices stand out in the cold.
Meanwhile, large touchscreens that work with gloves or buttons that are large enough for use with thick gloves help to make workers’ lives easier. Devices can also be vehicle-mounted for use in larger areas and deliver full connectivity to warehouse management systems so that staff do not need to waste time returning to an office to get their next task.
There is still room for human error, but with a solid management system the chances of any errors are reduced. In fact, by using instructions sent directly to a user’s device, staff can quickly adapt to situations in a way that an automated system cannot, whether its quickly changing location, dealing with unforeseen issues or handling ad-hoc requests.
A third option
No matter what stage of the decision process you are at, it’s worth considering a third option: a mix of automated processes alongside staff using rugged mobile devices.
In many ways it’s the best of both worlds. Most simple processes can be automated, freeing up valuable staff time to work on more important issues. A smaller rollout of automation reduces the initial cost and the risk involved.
A warehouse management system can help to oversee both the automated systems and staff using rugged devices, streamlining processes while staying flexible enough to deal with changing demands.
A system that offers a real-time view of inventory will offer cold store managers better visibility of their operation. But implementing a management system on top of a rollout of new technology can be a complex process.
However, with the support of a logistics expert it can be an easy transition that will ensure you are future-proofed. A good partner will look at the situation as a whole and design a solution that can be phased-in according to each unique site.
A trusted logistics expert that understands your business challenges can help you refine and establish your operational and strategic objectives and make the right choices regarding the best technology choices. They can also help with deployment and with any training that may be needed to work with specialist devices.
ABOUT THE AUTHOR - PETER MARSH
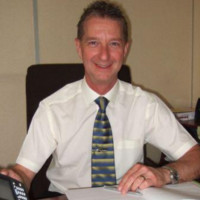
Peter joined TouchStar (formally Belgravium) in a sales
manager role in 2001. Prior to joining the
company, Peter held Partner and National Sales Manager roles within the parcel
and logistics industries.
In 2011 Peter was promoted to Sales Director and is now
actively involved in promoting the value of TouchStar’s Rugged Mobile Computing
solutions to the warehouse, logistics, manufacturing and field service
industries. When not involved in the business,
Peter is a keen and enthusiastic football and cricket fan.
ABOUT TOUCHSTAR
With over three decades of experience within the development of mobile computers for cold storage environments, TouchStar has the knowledge to confidently offer mobile computing solutions to successfully addresses key business issues.
TouchStar’s handheld, wearable, and vehicle-mounted mobile computers are purpose-built to provide enterprise level support for cold chain management needs. From labour-intensive assembly tasks to fully automated environments, TouchStar’s rugged mobile computers help reduce errors and significantly increase productivity in manufacturing operations.
Whatever area of manufacturing you are involved in, TouchStar’s rugged mobile computers provide the visibility of materials, parts and finished goods flowing through your manufacturing operations.
TouchStar offers extremely competitive prices on all its devices helping minimise procurement costs. TouchStar’s experts are just a phone call away to help you choose the right products for your needs.